Before the foundation comes, the right materials, hence most diaphragm wall construction companies pay high attention to the kind of concrete and slurry used in the construction process. With the right quality and quantity of materials, any construction can stand the test of time. One such vital material of the construction world is concrete, constituting refined and coarse aggregates mixed in a fixed quantity and water.
Though, selecting the right type of concrete is highly essential for any project as it can affect its strength, construction cost and time. This is why diaphragm wall contractors in India prefer using Ready-Mix Concrete (RMC) over Site-Mixed Concrete (SMC) for all deep basement underground construction.
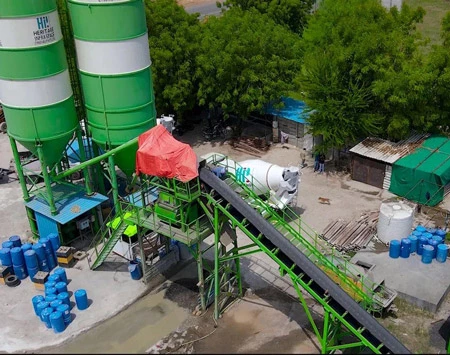
Ready-Mixed Concrete as its name connotes is a tailor-made concrete, manufactured in a plant and delivered to the site in a ready-to-use state. Depending on the specification of the construction project, RMC can be delivered in the plastic state (similar to the concrete dough) in a barrel truck or in the dry state to be mixed on the site itself.
On the other hand, the concrete mix prepared on-site is known as Site-Mixed Concrete. There are various components involved in the preparation of SMC in specific ratios to obtain the desired strength and consistency. Hence it needs to be done under the eye of an expert.
RMC for Diaphragm Wall Construction
Talking specifically about diaphragm wall construction, RMC with cement, sand, 10MM and 20MM aggregate, ad mixer, and potable water works most efficiently. The minimum cement content should range around 330 to 400 kg per cubic meter. It is vital to note that for any high water table or underwater project like diaphragm wall construction for dams, the cement content increases by 10%.
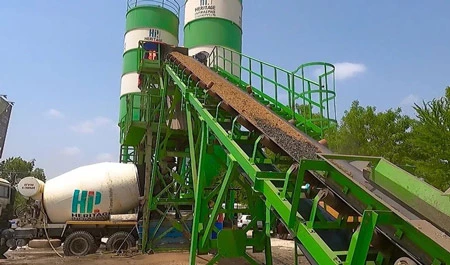
The RMC’s retention time is around 2.5 to 3 hours and can be maintained by using admixtures. To reach optimum workability it is advisable to maintain the slump around 170-190m. The top diaphragm wall contractors in India, suggest that the minimum grading should be M25 and M15 for a diaphragm wall and guide wall respectively.
Advantages of using Ready-Mix Concrete in Diaphragm Wall
The set standards maintained during the production of ready-mixed concrete by diaphragm wall construction service providers, like Heritage Infraspace Private Limited (HIPL), guarantee more durability and sturdiness to the infrastructure.
Apart from these, there are plenty of other advantages RMC holds above SMC. A few are listed below:
1. Better Quality Control
RMC provides consistent quality concrete since they are manufactured in a controlled environment of a plant equipped with sophisticated machines. With strict control over testing parameters and continuous monitoring, you get better quality control over the end product. Unlike SMC which is mixed at different locations on the site with inconsistent mixing techniques.
Hence, India’s leading diaphragm wall construction companies prefer using RMC over SMC.
2. Cost and time efficiency
The time involved in diaphragm wall construction materials can be saved with the use of Ready-Mixed Concrete. This is because RMC is made in large amounts with precise and uniform mixing methods removing the scope of remixing. It is also ready to use from the time they reach the site location with a retention time of only 2.5 to 3 hours.
Secondly, by using RMC you are cutting down on diaphragm wall construction costs as you no longer need additional equipment, cement, sand and other materials and additional experts.
3. Saves space
Using Site-Mixed Concrete will require you to set up large machines that take up more area than required for the construction. While many diaphragm wall contractors in India also manufacture, mix and deliver the required batch of Ready-Mixed Concrete to the specific site.
4. Reduced Wastage
To prepare a batch of SMC you will need cement, sand, water and other aggregates mixed in a specific ratio. If done wrong additional resources will be needed, sometimes leading to unnecessary wastage of resources. RMC plants use bulk concrete instead of individual cement bags. Additionally, the use of cementitious materials like admixtures reduces the amount of cement used.
How does HIPL source its concrete for diaphragm wall construction?
Heritage Infraspce has two fully automated plants located in the Hebatpur and Shilaj areas of Ahmedabad, with a capacity of over 60 and 1200 cubic meters per hour respectively. The German-technology Schwing Stetter RMC plants have transit mixers, stationary pumps, a chiller plant and a boom placer with a boom length of 37 meters.
Additionally, HIPL has an in-house testing lab and a team of experts to ensure the production of the best quality RMC.
This significantly reduces the diaphragm wall construction cost and aids HIPL to complete the project ahead of time.
The key motivation behind establishing our own RMC plant is to contribute significantly to improving the quality standards and setting a benchmark in the cement manufacturing industry. Additionally, support the ideas of quality engineering.
Frequently Asked Questions about Ready-Mix Concrete
Q1. Is ready-mixed concrete the same as cement?
Ans: Readymix concrete and cement are two different materials used in the construction industry. Concrete is a composite formed by mixing various materials, including cement.
Cement generally comes from sedimentary rocks and controlled chemical blends of natural elements like calcium, aluminium, Limestone and more.
Q2. What is ready-mix concrete used for?
Ans: Most prominently ready-mix concrete is used for big construction projects where on-site concrete mixing is not possible.
Q3. What are the types of RMC?
Ans: There are mainly three types of Ready-mix concrete (RMC):
– Transit mixed concrete
– Shrink mixed concrete
– Central mixed concrete
Their differences depend on the materials mixed in them.
To know how HIPL is building quality infrastructure reach out to us at info@heritageconstruction.in.