Concrete diaphragm walls play a pivotal role in diverse projects, including underground metro construction, multi-level deep basements for commercial centres and modern residential complexes. These subterranean installations create impermeable barriers, capable of supporting significant structural loads.
This article offers an exclusive glimpse into the daily workings of a diaphragm wall construction site. From workforce coordination to meticulous testing, we uncover the intricacies of each phase. Alongside, we delve into encountered challenges, underscoring the indispensable role of teamwork and strategic planning in the success of any diaphragm wall construction.
Assembly of Workers
The day on a diaphragm wall construction site kicks off with the assembly of the team that will be working on the site for the day. This team, usually numbering between 50 to 60 personnel, include:
- Steel and concrete labourers
- Welders and electricians
- Machine operators
- Site supervisors
- Project engineer
- Construction manager (usually on large-scale projects)
- Safety supervisors
Once all the above personnel have come together at their assigned call time, they’re divided into batches under their assigned managers/supervisors, who then provide them with safety equipment like helmets, welding glasses, safety boots and other gear. Sometimes there are client-appointed Project management consultants on the site too, in order to guide the team about specific requirements like top down construction.

Diaphragm wall construction in progress at the Central Secretariat in New Delhi
Preparing for Safety
Before commencement, a comprehensive safety briefing takes place. This session is conducted by the Safety Officer on the site and addresses the potential hazards linked to diaphragm wall construction, emphasising essential safety protocols. The workforce, equipped with modern equipment in diaphragm wall construction is given this refresher about safety protocols to ensure no untoward incident occurs during the construction. Construction techniques like vibro stone column techniques and top down construction require complete focus and clarity on safety measures. The teams are also encouraged to seek clarifications and voice concerns, ensuring a secure and informed work environment.
Work Flow Briefing
Following safety measures, a comprehensive workflow briefing ensues. This session delineates the day’s tasks, including the prioritised sequence of activities for concrete diaphragm walls. Anticipated challenges, if any, are highlighted, along with the strategies and utilisation of modern equipment in diaphragm wall construction to effectively tackle them. This proactive approach ensures a streamlined and efficient work process.
Inventory Accounting
Following the task briefing, meticulous inventory accounting takes place. This crucial step verifies the presence and operational status of essential materials and modern equipment in diaphragm wall construction such as machinery, rigs, safety items and tools required for erecting concrete diaphragm walls. An adept inventory manager meticulously tracks each item’s usage, conducts routine checks to ensure machinery maintenance and oversees the replenishment process. This proactive approach guarantees a seamless workflow, minimising disruptions and optimising construction efficiency on-site.
The construction of the diaphragm wall
Precise Excavation Process
The beginning of diaphragm wall construction involves meticulous excavation. This phase employs a specialised diaphragm wall rig, tailored for this purpose. This rig adeptly carves out a trench of the exact dimensions as the intended diaphragm wall.
Bentonite Slurry Injection & Reinforcement Setup
After trenching, a crucial step entails injecting a robust bentonite slurry. This clay-like substance bolsters trench walls and prevents groundwater intrusion. Simultaneously, a sturdy reinforcement cage, comprising steel bars, is precisely positioned within the trench to enhance the diaphragm wall’s structural integrity.
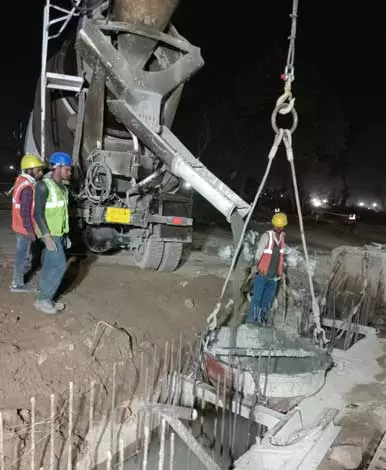
RMC being poured into the excavated area of the diaphragm wall
Pouring Concrete & Solidification
The casting phase follows, where concrete is methodically poured into the trench and left to solidify. This solidified concrete subsequently forms the robust diaphragm wall.
Rigorous Testing for Quality Assurance
Upon concrete solidification, rigorous testing ensues to validate adherence to design specifications. This can involve comprehensive load tests or assessments of water tightness, ensuring the diaphragm wall’s reliability.
Comprehensive End-of-Day Equipment Inventory
As the day concludes, a meticulous inventory process unfolds. All equipment and machinery, including specialised diaphragm wall rigs and crucial safety implements such as PVC water stoppers, undergo a comprehensive evaluation. This rigorous end-of-day inventory ensures optimal functionality and accountability, fostering the construction site’s efficiency and safety.
Challenges Encountered
There are a number of challenges that can be encountered during diaphragm wall construction. These challenges can include…
- Groundwater inflow: If groundwater enters the excavation area, it can weaken the ground and make it difficult to excavate the trench.
- Equipment failure: If the diaphragm wall rig or other equipment fails, it can delay the construction schedule and increase the cost of the project.
- Hazardous materials: There may be hazardous materials present in the ground, such as lead, asbestos or mercury. These materials must be handled carefully to protect the workers and the environment.
- Unexpected changes in soil conditions: The soil conditions may change unexpectedly, which can make it difficult to excavate the trench or install the reinforcement cage.
Teamwork & Planning is the Key
Despite the challenges, diaphragm wall construction is a safe and efficient way to construct retaining walls. At HIPL, we ensure we have an A-Team of experienced engineers and labourers who are experts in diaphragm wall construction. It is also important to have a well-planned project that takes into account the challenges that may be encountered.
HIPL has a team of experienced engineers and labourers who are experts in diaphragm wall construction. They also have a team of experienced project managers who develop well-planned projects that take into account the challenges that may be encountered. This is why HIPL is a leading diaphragm wall construction company in India.
Frequently Asked Questions
Diaphragm walls offer a number of benefits. They are very strong and can support the weight of heavy structures, they are watertight, which can prevent groundwater from entering a construction site, they can be used in a variety of soil conditions and they are relatively quick to construct.
Diaphragm walls are used in a variety of construction projects, including Metro railway station construction, top-down construction and vibro stone columns.
The time it takes to construct a diaphragm wall depends on the size of the wall and the ground conditions. However, it typically takes a few weeks to construct a diaphragm wall.
The costs associated with diaphragm wall construction vary depending on the size of the wall, the ground conditions and the location of the project. However, diaphragm wall construction is typically more expensive than other types of retaining wall construction.
You can read up about the various diaphragm wall projects we have worked on all over the country, for private sector developers and government projects too. You can also reach out to us at info@heritageconstruction.in to plan a meeting with us and for quotes on your upcoming projects requiring deep basements and diaphragm walls.